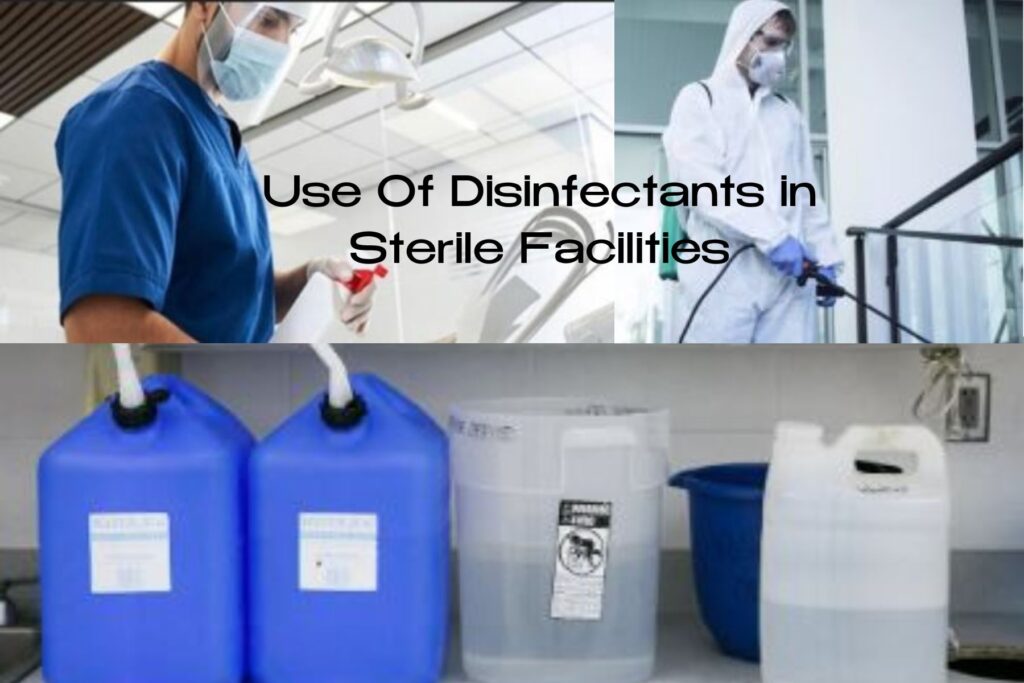
Use Of Disinfectants in Sterile Facilities of in Secondary Pharmaceutical Facilities
The use of disinfectants within sterile facilities, particularly the critical areas such as grade A/B areas, requires some additional precautions. For example, solutions will need to be filtered into the aseptic filling area through sterile 0.2µ membrane filters. However the general principles outlined in previous sections still apply, using the same disinfectants, controls in separation and rotation of agents. The additional requirements are summarized below:
Cleaning and disinfection of critical areas such as the grade A/B areas, will be very frequent, at least daily during operation in the area and at critical zones such as filling head or within the filling cabinet after any intrusion or spillage (usually with non residual sprays such as 70% alcohol). The introduction of disinfectant solutions into sterile filling areas should be with the same precautions as for products and other liquids. This means they should be sterilized, the usual method being by membrane filtration. Some commercially available solutions (for instance 70% Alcohol sprays) may be provided as a sterile disposable pack such as a spray which are double wrapped and frequently have been sterilized by irradiation. These packs are acceptable although the supplier should provide assurance of sterilization and individual packs should be checked for any damage to the packing (and rejected if necessary). Several companies now provide pre-sterilized disinfectant concentrates (filtered, double bagged and
irradiated) enabling preparation, usually in filtered Water for Injection, within the sterile area.
The membrane filters used for disinfectant solutions in sterile operations must be sterilizing grade (0.2µ or equivalent) and integrity tested. As many disinfectant solutions are surface active they may well significantly change the acceptance value for the integrity test (e.g. bubble point may be substantially depressed). The integrity test value for the disinfectant solution should be determined experimentally (the supplier of the filter will often have data) although the filter membrane does not require the level of validation performed for products. Routine testing of filtered disinfectant solutions at or close to the end of the shelf life, should be included in the environmental monitoring programme. This will include bioburden testing and swabs of the external surface of containers.
Full batch documents should be retained for disinfectant solution preparation and a shelf life applied. For aqueous general disinfectant solutions it may not be acceptable to hold these for any length of time in the grade A/B areas and they may be best prepared on a daily basis. Sprays which may contact with machine product parts, for instance within filling cabinets, must evaporate quickly and leave no residues which could enter the product. This in reality restricts the materials for these critical situations to alcoholic solutions (70% IMS, denatured Ethanol, IPA in water. The water quality is recommended to be Water for Injections). If commercial sprays are used, it is advisable that these are also manufactured with Water for Injection.
The written procedure for disinfection and cleaning of areas within sterile facilities must specify a method for inclusion of any recommendations (generally made by Microbiology or QA) for additional cleaning and special treatment where out of compliance results are obtained. An environmental monitoring programme is required for the sterile manufacturing facility. This programme should ensure the identification of any non-compliant results and ensure actions are taken to rectify such incidents. The programme, often incorporated in a formal manual, will recommend disinfectants for routine cleaning and frequency of their rotation, as well as routine microbiological
assessment of disinfectant solutions.