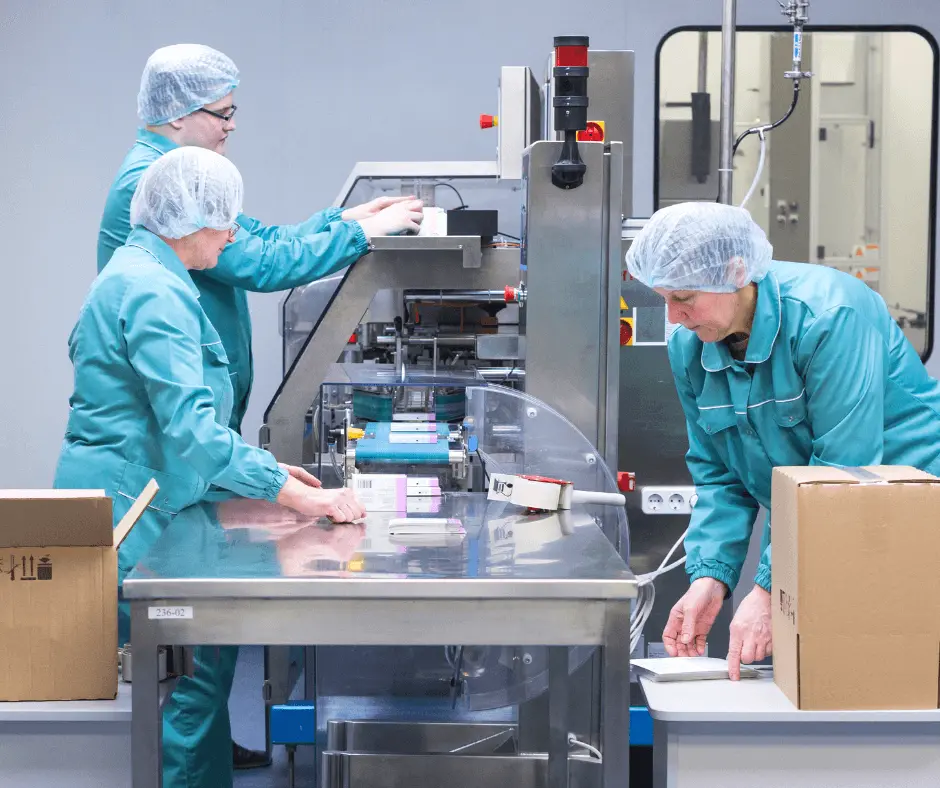
Tips to Develop Equipment Cleaning Procedure in Pharmaceuticals
Quality management in pharmaceuticals is a critical factor to both the pharmaceutical companies and the public at large Through this article, the following tips will be crucial to developing the equipment cleaning procedure for use in the pharmaceutical industries:
Cleanliness of equipment in the pharmaceutical manufacturing processes is very important so as to meet quality standards, minimize risks from contamination and also meet the regulatory requirements. Proper equipment cleaning process is of out most importance when providing medications to the public due to the essence of quality and safety. In this article, the reader will find the main steps a
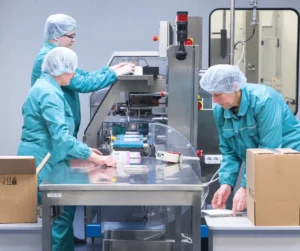
nd recommendations for proper establishment of the equipment cleaning process in the pharmaceutical industry.
Why Equipment must be cleaned in Pharmaceuticals?
The pharma sector functions according to high regulatory standards because it is all about manufacturing products that will ultimately be consumed by people. Of these regulations, cleaning processes of manufacturing tools are critical. Unclean equipment fosters cross-contamination, production of low quality or tainted products, hazardous drug remaining on the tools can be a danger to patient health and the environment as well.
Key reasons why equipment cleaning is crucial include:
1. Preventing Cross-Contamination: This is a process whereby residuals from one product infect another batch of a distinct product type. This is much more damaging when it concerns strong medicaments including antibiotics, hormones and biologic preparations capable of dangerous effects in case traces remain on the equipment.
2. Regulatory Compliance: Both FDA, EMA, and WHO polices for the cleanliness, sanitation, and validation procedures tightly in biotech industries. A non-compliance may be subjected to fines, withdrawal of some products on the market, or closure of facilities.
3. Maintaining Product Quality: Contaminated instruments pose a great threat because they influence the purity and effectiveness of the pharmaceutical products. Impurities may alter the structure or solubility of drugs making them ineffective for use in treatment of infections.
4. Ensuring Worker Safety: Any remains on the equipment either chemical or the active ingredients present could be dangerous to the workers. Heating can cause health problems or an occupational accident, such as inhaling toxic substances or coming into contact with toxic substances through the skin.
5. Extended Equipment Lifespan: Cleaning also means that machinery used in manufacturing will not be exposed to too much wear and tear, hence will also lead to effective and efficient functioning of manufacturing equipment.
Overview of Measures When Designing Equipment Cleaning Protocols
Formulating a good cleaning process is a several-step process that always has to consider all the crucial factors and should be performed following all the rules of hygiene. Below are the essential steps for creating a cleaning procedure:
1. Know the Required Cleaning Procedures for Several Equipment’s
The first activity that must be followed in establishing cleaning process is to identify the appropriate cleaning requirements for the corresponding equipment in question. Severally, apparatus that is used varies in how it can be cleaned or disinfected. For example:
Mixing tanks: May need to be washed with solvents and then scrubbed to remove all the residues of raw materials.
Tablets or capsules manufacturing machines: They very often require special cleaning to avoid cross contamination of active ingredients.
Filling machines: Recommend stringent washing to minimize the risk of carry over from residues left in the pipes, nozzle or containers.
Every type of equipment should therefore be examined on the likely contaminants it may contain, the type of product it deals with, and appropriate cleaning materials.
2. Cleaners Choice
The kind of agents to use in cleaning are among the most crucial aspects in achieving good cleaning. The cleaning agents should be effective enough to clean the contaminants without spoiling the equipment’s. The following factors should be considered when selecting cleaning agents:
Type of Contamination: Some of the contaminants are organic, inorganic, microbial, and thus need different cleaning agents to dislodge from the surface. Organic residues may need solvents for effecting leaching while mineral residues may need either acids or alkaline leaching agents.
Compatibility with Equipment Materials: Make sure that the cleaning agents can not harm the equipment in terms of wearing or corroding it. For example, an effective cleaning agent for the stainless steel equipment should not be corrosive and should be appropriate for equipment’s that are used in the manufacture of pharmaceuticals.
Environmental and Safety Impact: It means that concerns of selecting cleaning agents must include the effect on environment and potential risks for workers. If possible, only agents that are non-toxic and otherwise biodegradable should be used.
Effectiveness: The selected cleaning agent must clean surfaces and other substrates to remove all types of residues, but it has to do so without leaving behind any elements that may harm the ultimately product.
3. Cleaning Procedures and Protocols
After the equipment types as well as cleaning agents are chosen, the next thing to decide is cleaning process. This basically entails making a procedure checklist which should be used each time the equipment is cleaned. An effective cleaning protocol should include the following:
Pre-cleaning Inspection: Assess the equipment in order to detect areas of discoloration that require more delicateness in the cleaning process.
Cleaning Procedure: It is also important to indicate in details the preparation of cleaning aids, methods of applying cleaning aids and the approaches used in cleaning.
Cleaning Parameters: What is important in defining the parameters that will guarantee cleaning? These include:
Cleaning time: The length of time for which the cleaning agent should be used.
Temperature: The temperature of the cleaning water in which the cleaning agent achieves its best performance.
Concentration: How the right amount of the cleaning agents to be used should be determined.
Post-Cleaning Inspection: However, before using the equipment, ensure that no residual substances are left on the surfaces of the tools. This can be done by performing a gross visual assessment, or through more rigorous chemical analysis such as swathing, where a swab is rubbed on a surface, or rinse sampling which involves rinsing a part with water.
4. Upgrade Cleaning Processes
Verification is an important activity of cleaning to confirm the efficiency of the cleaning processes. Validation proves that if the process of cleaning is repeated the results will always be as required by the law and the quality standards. The validation process includes the following:
Development of Validation Protocols: These directives provide the standards and steps by which the capacity of the cleaning process can be evaluated.
Testing Methods: As it was mentioned before, cleaning validation can be performed using the following Approaches:
Swab Sampling: After cleaning the equipment a swab is made to detect if there is any sign of contaminants on the equipment.
Rinse Sampling: The rinse water sample is analyzed for the presence of contaminants.
Visual Inspection: Check on the visibly dirt or deposits on the equipment.
Microbiological Testing: Evaluate the status on microbiological contamination, especially where working in a sterile area.
It also found that transforming an assortment of processes into a procedure that is routinized should involve as many cleaning cycles and tests as possible to guarantee that the procedure works every time.
5. Make a Cleaning Plan
A cleaning schedule also makes it easier to make sure that equipment has been cleaned to a required standard and to a set frequency. The schedule should take into account the following:
Frequency of Cleaning: There are machines may require the cleaning after every batch and there are those which will need cleaning after a week or a month. The following factors should guide the schedule; The usage of the equipment and processing of products.
Priority of Cleaning: Hardware that has high risk of contamination due to its interaction with highly potent or hazardous materials should undergo cleaning much often than equipment with minimal risk of contamination.
Post-Production Cleaning: Some of the equipment require washing immediately after completion of one batch of production, when converting from one product or formulation to another.
6. Consistent Education and Standard Operation Procedure (SOP)
It is therefore desirable that the cleaning process be well documented and follow a strict sequence to limit variations as well as confirm to current regulatory policies. To achieve the desired results in cleaning it is very important to have set Procedural manuals as they will help in formulating the right SOPs. The SOPs should include:
Step-by-step Instructions: Specific ways on how to clean each of the equipment in question.
Roles and Responsibilities: Identify persons who are supposed to be cleaning various aspects of the environment.
Documentation: Always maintain the records of any cleaning conducted in the organization in which you record the date, the personnel involved and cleaning validation results when applicable.
Staff training is also very important. Everyone involved in the operation and/ or cleaning should be familiar with the SOPs and the reasons behind proper cleaning as well as how to use the cleaning products safely. Tailor made training particulars should be arranged at least once a year to ensure all aspects of new procedures and regulations have been reviewed.
7. Cleaning Processes: Surveillance and Enhancement
However, after implementing the equipment cleaning procedures some level of monitoring and evaluation is highly recommended. Incorporate monitoring and evaluation mechanism to the effectiveness of the cleaning working and conduct periodic analysis of the working to optimize the working.
Cleanliness, inspection, and validation data collected from cleaning personnel and group performance should be compared for set corrections. Such schedules will have to ensure that either internally or externally, the cleaning procedures used are up to date with the standards and with changes in requirements.
Conclusion
It is becoming apparent that an effective equipment cleaning procedure in the pharmaceutical industry needs to be well rounded and strict industry standards need to be met for the products, workers, and regulation purposes. Following these measures, that include recognizing cleaning expectations, choosing appropriate cleaning agents, paperwork of cleaning procedures, assurance of cleaning process, development of an appropriate cleaning timetable, a cleaner and less contaminated equipment can be achieved. Regular supervision, education as well as constant updates to the system will assist in maintaining the cleaning method optimally effective and in line with the set guidelines. Integrated and effective procedures of cleaning can help the pharmaceutical manufacturers to sustain high quality of their products as well as to meet all the mandatory requirements of regulations.