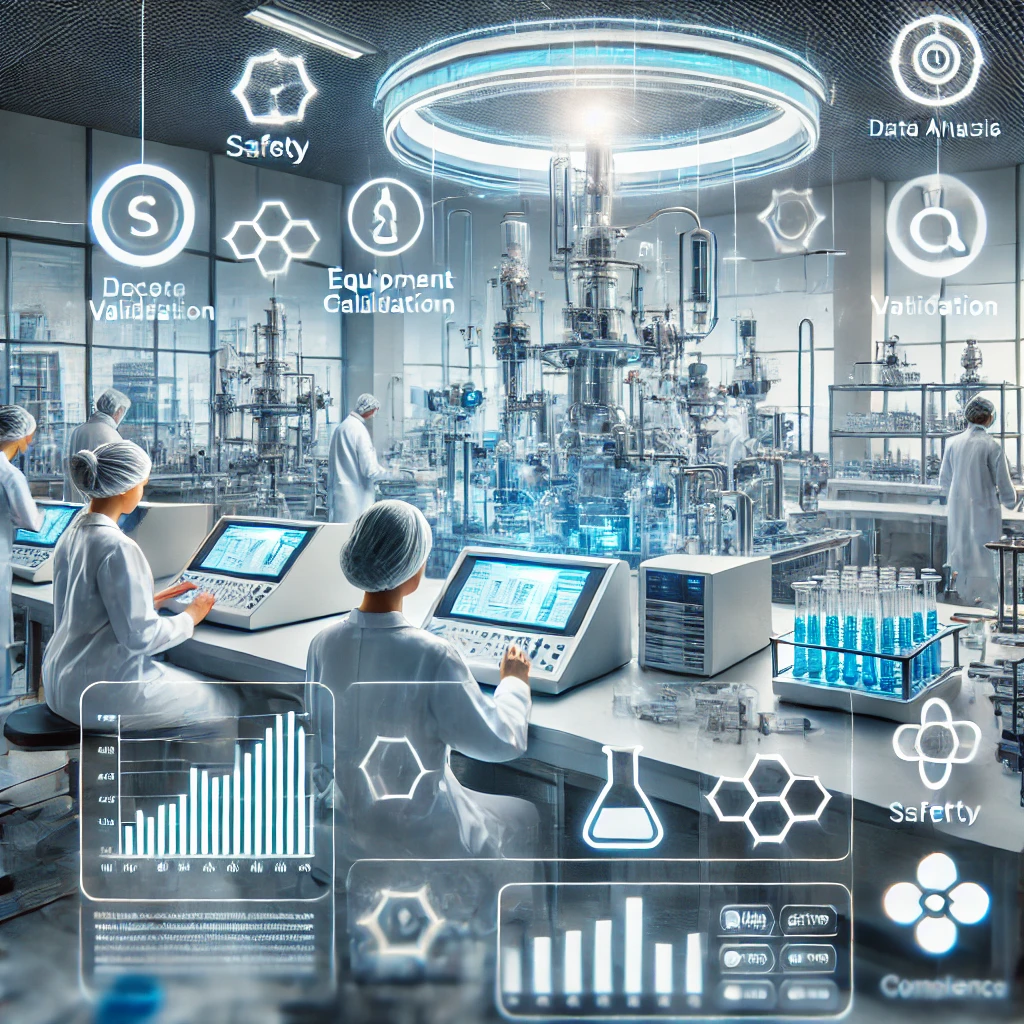
Revalidation of pharmaceutical processes
Introduction
The pharmaceutical line of business has evolved significantly since it was started Trading. Due to enhancing need for quality and safety of drugs, frequent evaluating of the processes used in the production of these drugs has become a critical issue. Practical approach to achieve this objective as highlighted involves revalidation of pharmaceutical process.
In the pharmaceutical context revalidation can be described as the check of all processes, systems, and procedures to verify their continued efficiency and relevance to the current regulatory requirements, guidelines, and standards. The idea of revalidation is to ensure that the manufacturing process is adequate and acceptable, thereby providing patients and stakeholders with confidence in products which they depend upon. This Document will explore the reasons why the pharmaceutical processes need to be revalidated, describe the major steps of the process, and consider the purpose of revalidation in terms of achieving and maintaining excellence in the pharmaceutical production.
The Role of Staff Revalidation to the Growth of the Pharmaceutical Industry
This paper further shows that revalidation is an important aspect of quality assurance in the pharma industry. Therefore, the revalidation of pharmaceutical processes is critical for sustaining up to date manufacturing standards for assuring product quality and patient safety and overall public health.
1. Ensuring Quality and Safety
The goal of the revalidation is the validation of the manufacturing process that has been chosen by the company in order to keep checking that the process provides high quality of medications as it was established before. Additionally, it also continuously assesses processes and systems for any abnormalities, so they are amended on the spot. Such a reconsideration of processes may come up with threats and mistakes which will help reduce the chance of putting to the circulation products or drugs.
2. Demonstrating Compliance
Apart from giving an assurance that products are safer and of better quality, revalidation enables an organization to satisfy cGMP, ICH and other standard guidelines. By making sure that processes are contained by these standards organizations reduce the risk of running afoul of the regulators, fines, and even plant shutdowns.
3. Maintaining Efficacy
Therefore revalidation facilitates the continual effectiveness of the pharma products in the preservation of their therapeutic value. It shows that by regularly updating their processes based on new research and technologies as well new rules and regulations they can keep the effectiveness of their products constant and ensure that they are up to date with the newer forms in the market.
Understanding Revalidation Revalidation Process and its key steps
The process of revalidation involves some important stages which have to be executed correctly to enable the Company to organize an accurate and effective review.
1. Planning
The first type is planning the revalidation process. Reviewing it involves examination of the scope of areas covered in the review, followed by setting the goal and sizing the period of executing the review process. In addition, during the planning phase, it is also very important that during the same run all the departments to be taken into consideration, so that not a single body can feel left behind.
2. Document Review
Subsequently, all the previous records about the manufacturing process have to be studied carefully. This includes batch records, process validation reports and documents, satisfactory quality control data and records. Thus, looking at the contents of such documents one can judge if any modifications are to be made in terms of compliance with the current standards and standards.
3. Process Evaluation
The third step is based on how efficient a manufacturing process is or the effectiveness of manufacturing process. This may involve seeing it in operation, checking equipment effectiveness and analyzing results of continuing quality control surveys. This step also solves for smoothening and enhancing the processes through realization of possible areas that may require enhancement.
4. Risk Assessment
The period of revalidation also involves a risk assessment plan. This entails the process of risk assessment comprising of risk identification, assessment for risk likelihood and risk magnitude. If all these risks are tackled in an early stage, then there is no way they will grow out of proportion and inconvenience the manufacturing process.
5. Implementing Changes
From the results of the revalidation, possible changes may be required in the manufacturing process of the particular product. These changes should therefore be well recorded, and effect on product quality and safety discussed as well. The implementation should be done in accordance with trained personnel, and supervised well S to reduce problems that might be encountered during the process.
6. Validation and Verification
Validation and verification is the last process of revalidation. It is the last step in the list of which the final one is a validation step, to see if the changes that have been made to the process, are delivering a stable output. Verification, however, is that the production process conforms to all legal and standards required it be, and verification does this.
Conclusion
Pharmaceutical processes must therefore be revised periodically to ensure that the pharmaceutical Industry meets required standards as needed. One the one hand revalidation should be seen as an important process for compliance with rules, quality and safety of good and drug effectiveness for the public health. It may be as an asseveration that by the systematic implementation of one’s revalidation strategy, one can rest assured that the processes that are vital to the workings of one’s entity are not only efficient and safe, but also current in this fast-paced, constantly evolving global market, and hence deliver vital medications to the populace who needs it most.