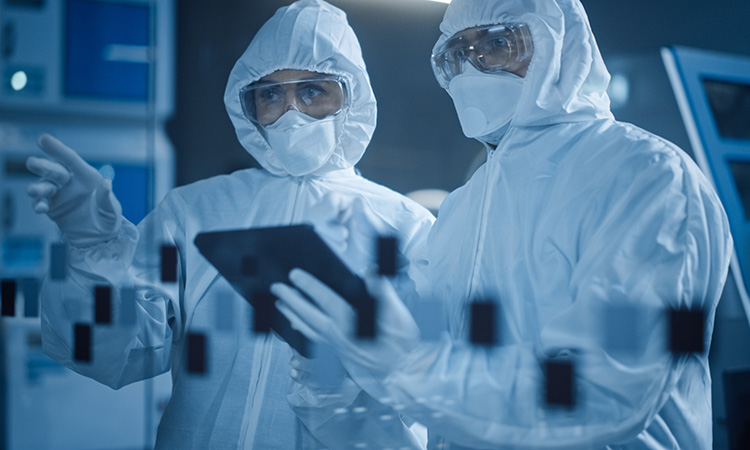
Requirements of FDA for Training in Pharmaceuticals
The pharmaceutical industry operates in a highly regulated environment where adherence to stringent quality and safety standards is essential to ensure the production of safe, effective, and high-quality products. Among these regulations, the U.S. Food and Drug Administration (FDA) places a significant emphasis on employee training. Comprehensive and well-structured training programs are pivotal for maintaining compliance, reducing errors, and enhancing overall operational efficiency. This article explores the FDA requirements for training in the pharmaceutical industry, highlighting key aspects, best practices, and compliance strategies.
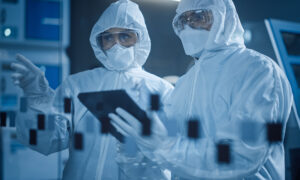
Understanding FDA Training Requirements
The FDA mandates that pharmaceutical companies establish and maintain robust training programs as part of their regulatory compliance obligations. Training ensures that all personnel involved in manufacturing, testing, and quality assurance activities are knowledgeable and competent in their roles.
Key Regulations Governing Training
- 21 CFR Part 211 (Current Good Manufacturing Practices – cGMP):
- Subpart B – Organization and Personnel:
- Section 211.25(a): “Each person engaged in the manufacture, processing, packing, or holding of a drug product shall have education, training, and experience, or any combination thereof, to enable that person to perform their assigned functions.”
- Section 211.25(b): “Training shall be in the particular operations that the employee performs and in cGMP as they relate to the employee’s functions.”
- Subpart B – Organization and Personnel:
- 21 CFR Part 820 (Quality System Regulation for Medical Devices):
- Applicable to pharmaceutical companies producing combination products, this regulation requires documented training in quality management systems.
- FDA Guidance Documents:
- Various FDA guidance documents emphasize the importance of training in quality management, data integrity, and process validation.
Core Components of an FDA-Compliant Training Program
A robust training program addresses several critical components to ensure compliance with FDA regulations.
1. Initial Training
- New Employee Orientation:
- Covers company policies, quality culture, and regulatory expectations.
- Role-Specific Training:
- Focuses on job-specific responsibilities, including standard operating procedures (SOPs), equipment operation, and safety protocols.
2. Ongoing Training
- Continuing Education:
- Regular updates on changes in regulations, new technologies, and advancements in processes.
- Refresher Training:
- Periodic reviews of essential knowledge areas to reinforce best practices.
3. GMP-Specific Training
- Training on cGMP principles and their application in daily operations, including:
- Proper documentation practices.
- Hygiene and contamination control.
- Deviation management and CAPA (Corrective and Preventive Actions).
4. Training on Quality Systems
- Includes training in areas such as:
- Quality risk management.
- Data integrity and electronic records management.
- Change control and validation.
5. Documentation of Training
- Accurate records of all training activities, including:
- Training materials used.
- Attendance records.
- Assessment results and certifications.
Best Practices for Meeting FDA Training Requirements
Compliance with FDA training requirements is not just about meeting regulatory expectations; it is about fostering a culture of quality and continuous improvement. Here are some best practices:
1. Develop a Comprehensive Training Plan
- Outline training needs based on job roles and responsibilities.
- Include a timeline for initial and ongoing training.
- Ensure alignment with current FDA regulations and industry standards.
2. Customize Training Programs
- Tailor training content to specific job functions.
- Use real-world examples and case studies to enhance relevance and engagement.
3. Leverage Technology
- Implement Learning Management Systems (LMS) to:
- Track training progress.
- Automate reminders for upcoming training sessions.
- Store training records for easy retrieval during audits.
4. Engage Experienced Trainers
- Use qualified internal or external trainers with expertise in GMP, quality systems, and regulatory compliance.
- Encourage interactive learning through workshops and practical demonstrations.
5. Assess Training Effectiveness
- Use pre- and post-training assessments to evaluate knowledge retention.
- Gather feedback from participants to improve future training sessions.
6. Regularly Review and Update Training Programs
- Adapt training content to reflect:
- Changes in FDA regulations.
- New product introductions or process changes.
Common Challenges in FDA Training Compliance and How to Overcome Them
Despite the critical importance of training, pharmaceutical companies often face challenges in achieving full compliance with FDA requirements.
1. High Employee Turnover
- Challenge: Frequent staff changes can disrupt training continuity.
- Solution:
- Maintain a pool of pre-recorded training sessions for quick onboarding.
- Use cross-training to ensure multiple employees are qualified for critical roles.
2. Lack of Training Resources
- Challenge: Limited access to qualified trainers and training materials.
- Solution:
- Partner with industry associations and training providers.
- Invest in digital training platforms.
3. Inadequate Documentation
- Challenge: Missing or incomplete training records during FDA inspections.
- Solution:
- Use automated systems to track and archive training data.
- Conduct regular internal audits to ensure documentation completeness.
4. Resistance to Training
- Challenge: Employees may view training as a burden.
- Solution:
- Highlight the importance of training in career growth and compliance.
- Incorporate gamification and incentives to increase participation.
Consequences of Non-Compliance with FDA Training Requirements
Failure to comply with FDA training requirements can have severe repercussions for pharmaceutical companies, including:
- Regulatory Actions:
- Warning letters.
- Form 483 observations.
- Product recalls or plant shutdowns.
- Financial Losses:
- Fines and penalties.
- Increased costs due to corrective actions and retraining.
- Reputational Damage:
- Loss of trust among stakeholders, including patients, healthcare providers, and regulators.
- Operational Disruptions:
- Delays in production and supply chain interruptions.
FDA Expectations During Inspections
During inspections, FDA investigators assess the adequacy of training programs by reviewing:
- Training records for all employees.
- The alignment of training programs with job roles.
- Documentation proving the effectiveness of training efforts.
- The frequency and content of GMP training sessions.
Companies should be prepared to:
- Demonstrate a clear training plan.
- Provide evidence of continuous education initiatives.
- Show proactive measures taken to address training gaps.
Conclusion
Training is a cornerstone of regulatory compliance in the pharmaceutical industry. The FDA’s requirements emphasize the need for well-structured, role-specific, and continuously updated training programs to ensure that personnel are competent and compliant with current regulations. By adopting best practices, leveraging technology, and fostering a culture of quality, pharmaceutical companies can not only meet FDA expectations but also drive operational excellence and enhance product quality. The investment in robust training programs ultimately safeguards public health, builds stakeholder trust, and reinforces the industry’s commitment to excellence.