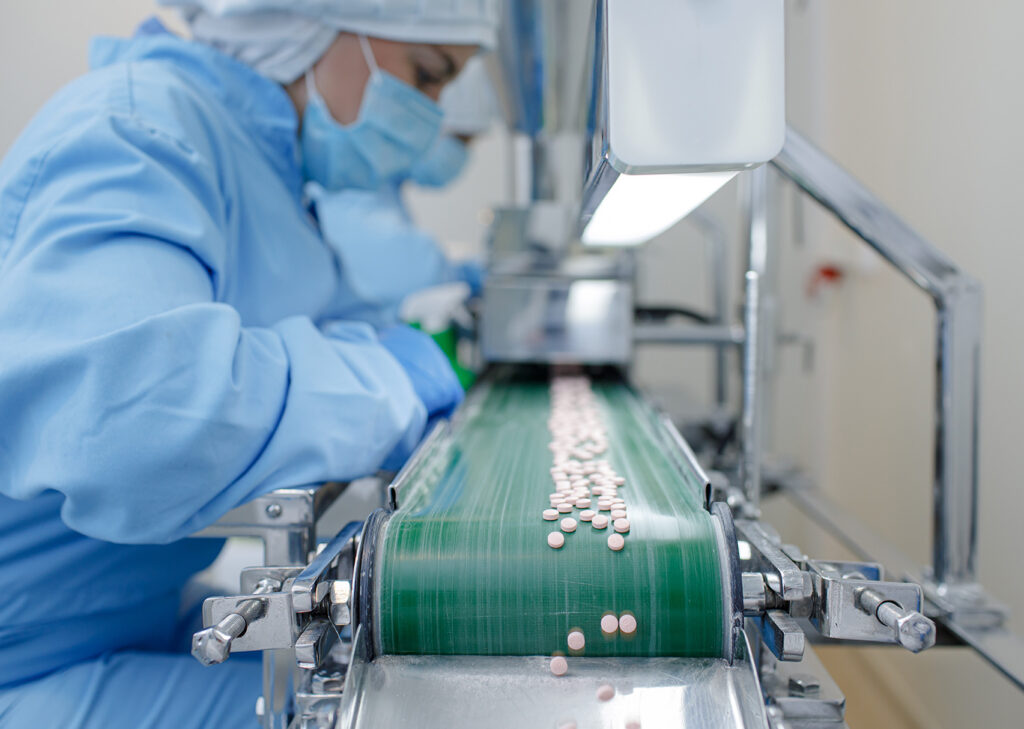
Quality Inspection in Pharmaceuticals: Ensuring Product Safety and Efficacy
Quality Inspection in Pharmaceuticals: Product Safety and Efficacy, Purity, potency, and quality of drugs where the primary concerns which must be met in pharmaceutical manufacturing. Supervision also features rapidly as the central method of ensuring desirable quality in raw materials, work in progress, and finished products throughout the stages of purchase, manufacturing, and sale. Proper quality inspection measures facilitate the delivery of nice products that are safe to use, as well as conform to standard set by the authorities, which are not contaminated or possess any form of defects.
Consequently, this article will proceed with a detailed analysis of quality inspection in the frame of the pharmaceutical industry, pinpoint its significance, primary stages, diverse sorts of quality inspections, and recommended efficient practices for achieving the utmost pharmaceutical product quality.
Why is Quality Inspection Important Particularly in the Manufacturing of Pharmaceuticals?
Pharmaceuticals industry is unusual in the sense that it is medicine that affects directly the health of people. Consequently, quality of products is a point that cannot be compromised. Legal authorities including the FDA, EMA, and the WHO have set high standards that have to be met before a new drug is released to the market to produce quality pharmaceutical products.

Quality inspection is crucial for several reasons:
Safety and Efficacy: A pharmaceutical product must undergo a lot of scrutiny to be accepted in the market place. Quality inspection is a confirmation that the products are safe for human consumption and that they have met their required performances.
Compliance with Regulatory Standards: Bureaus demand and expect multinational corporations of pharmaceutical industries to follow certain standards of production, presentation, and packaging. Such legal requirements have to be complied with through timely quality inspections to reduce on costly fines, product recall and court cases.
Preventing Contamination: Medicinal products are vulnerable to contamination from sources of contamination which can be raw materials, manufacturing processes and packaging. Quality inspection plays its critical role in issue identification and eradication in order to avoid contamination and attain levels of purity.
Maintaining Brand Reputation: Complex and sophisticated products can be achieved through a framework, fulfilling the customer expectations, maintaining trust as well as the satisfaction of healthcare providers and licensing bodies. Quality inspection also helps pharmaceutical companies so that they can uphold their brands besides making their customers confident.
Reducing Costs: Getting to identify any developmental problems during the manufacturing process helps organizations to rectify them as early as possible so that the occurrence of major issues such as product recalls or regulatory fines is avoided besides minimizing waste.
Check Points in Pharmaceutical Quality Inspection
Pharmaceutical quality inspection includes several main steps aiming to reveal possible problems in both, the material used and the product manufactured. Below are the primary stages of the quality inspection process:
1. Raw Material Inspection
This is the main reason why the selection of parts that require putting in the production line has to be of the highest standard. The first level of quality control is examining the raw materials accepted for usage in production. APIs, excipients, packaging material and other items which are used in formulation of drug and therapeutic products.
Key aspects of raw material inspection include:
Supplier Qualification: Suppliers of raw materials participating in the production process must meet the GMP requirements and have gone through the required sociability test.
Material Specifications: Ensuring the materials fit the more general requirements of the regulatory standards frameworks as well the internal quality standards.
Incoming Testing: Carrying out various test on various batches of raw materials to determine the purity, identity and quality of the raw material.
Documentation: Ensuring that all batches of raw materials received come with Certificate of Analysis (COA) to confirm quality of the material.
2. In-Process Inspection
These type of inspection is done on the process when the product is still being made with controlling of production in mind. Such probing is crucial in any case to ensure that no problem may occur throughout formulation, mixing, packaging, or any other manufacturing processes.
Key aspects of in-process inspection include:
Monitoring Critical Control Points (CCPs): Finding out areas in the process that are most influencing the quality of the final product (e.g., temperature, humidity period of mixing etc).
Visual Inspection: Ensuring that there are no physical items within a product, that some of the formulations are incorrect or that the manufacturing procedures being followed do not meet the required standards.
Sampling and Testing: Taking samples blindly in different stages of the manufacturing process and testing them in order to make sure that the they are of correct quality.
Equipment Calibration: Inspecting and monitoring the performance of manufacturing equipment to guarantee that products produced by the equipment are within a given permissible variance.
Environmental Monitoring: Determining which manufacturing areas have been contaminated, or not contaminated, and the extent of contamination in aseptically or a sterilized manufacturing areas as the case may be.
3. Final Product Inspection
The final product inspection safeguards the quality of the pharmaceutical manufactured product to the producers before it is taken out to the market. This stage of inspection is very important in as much as it dictates whether the product can be useful in the intended condition or not and whether it is safe to be taken.
Key aspects of final product inspection include:
Physical and Chemical Testing: In field tests, round-robins, challenge or sentinel, and innovative investigations, the benefit of which includes making tests to determine the physical and chemical characteristics of a product like its appearance, potency, rate of dissolution, and chemical content.
Microbial Testing: As for the sterile products, microbial sampling facilitates objective determination of the presence or absence of microbial pathogens within the subject product.
Packaging and Labeling Inspection: Assuring oneself that seals on the outer layers of the packaging are not broken; that words on the labels are not in any way changed and that all necessary words are inscribed (for instance, the date of expiry, the batch number, the dosage details).
Stability Testing: Is aimed at confirming that the product is going to remain effective and safe for the time it is expected to be on the shelf through determining it stability at different environmental conditions.
4. Batch Release and generation of Documentations.
The product batch requires release for distribution after it has received the final point check at the production line. Organizational checklists summarize all necessary tests, inspections, and validation before product release and should be reviewed. This includes:
Reviewing Batch Records: The process of every produced document is ensuring that it is complete and accurate with the regulatory requirements.
Certificate of Analysis (COA): The COA gives a report of the results of the test besides the quality features of the batch of the product.
Approval for Release: The batch must also be released by some signatories of an authorized person, which can be the QP.
5. The Post-Market Safety Monitoring can be continued.
The post-market surveillance becomes inalienable after launch of the pharmaceutical product with a view of ascertaining whether the product serves its intended purpose or may harm the consumers. This includes:
Adverse Event Reporting: The reporting of any untoward reactions or side effects that may be traced to the use of the product.
Consumer Feedback: Outlining problems where quality may be compromised through involving the consumers and other healthcare givers in giving their feedback.
Periodic Audits and Inspections: Performing timely surveys of manufacturing plants together with the guidelines for production procedures and compliances.
There are basically two broad categories of Quality inspections involved in any pharmaceutical manufacturing line these include:
Quality inspections can be performed at any point during the manufacture of pharmaceuticals and each type differs in its purpose. These inspections can be categorized into the following types:
1. Visual Inspection
The visual inspection is the initial kind of the quality control; it is also called the bare eye inspection. It entails close inspection of the product to possibly detect some vices that include: foreign particle, wrong labeling, wrong packaging among others. This inspection is usually done while inspecting both, in-process and final product examinations.
2. Physical Inspection
Physical inspection means the examination of physical characteristics of the product for instance size, shape, weight and texture. For solid dosage forms such as tablets or capsules, these may involves assessment of size homogeneity and weight, and tablet hardness and friability.
3. Chemical Testing
In chemical testing, the chemical make up is determined in order to check for compliance to the recommended levels of the active therapeutic agents as well as other ingredients. Most of this testing is carried out in the final inspection of the actual product.
4. Microbiological Testing
Microbiological tests are important for sterils pharma in order not to release products with microbial contamination. It covers examination of pathogens and presence of pathogens in products sold to consumers.
5. Dissolution Testing
Especially, dissolution profiles are applied when the dosage forms are prepared as tablets and capsules; the rate of API dissolution in a solution is investigated. This test will guarantee that the product will release the API at the right time so that its absorption in the body is ideal.
6. Stability Testing
Stability testing is conducted as a means of determining how a product will remain stable in the course of its storage. These comprise potency of the product, the rate of dissolution of the active ingredients and the physical characteristics of the product during its shelf life.
Recommendations for quality control inspections in the pharmaceuticals
To ensure the highest standards of quality inspection, pharmaceutical companies should follow these best practices:
Adherence to GMP: Only GMPs can be implemented in order to maintain consistency of all inspections on the client’s part and compliance with the applicable regulations.
Training and Competence: Specialist quality inspectors must be fully knowledgeable on all tests and regulatory standards as well as the proper ways of conducting the inspection.
Automated Systems: The adoption of Automated inspection system cuts across a number of sectors to enhance accuracy, minimize human error and enhance automation of the inspection process more especially on the visual and physical inspections.
Regular Calibration: Guarantee a high level of functional maintenance of all testing equipment, including laboratory equipment and testing/inspection devices.
Continuous Monitoring: The production environment, the equipment and the process all should be closely monitored and if there is something wrong with them, then corrections have to be made before it goes wrong with the product.
Documentation and Record-Keeping: It is important to keep records of all the inspections carried out, test results, as well as details of all corrections made. It is very important in areas of compliance and audit trail.
Risk-Based Approach: Appl utilizing a risk assessment approach to quality control/ inspection that targets higher risk areas of concern that might affect quality of the product, patients, etc.
Conclusion:
Pharmaceutical manufacturing, therefore, should include quality inspection, which identifies and regulates the safety, efficacy and quality of pharmaceuticals. Starting from the receipt of the raw materials to the packaging of the final product, all the stages of manufacture involve serious quality control. Through learning of the different guidelines and following them diligently in the course of developing its products, various firms in the production of pharmaceutical products can minimize on the likelihood of having their products contaminated as well as ensuring that their products are safe for use among the consumer society. It is only important for these pharmaceutical firms to embrace the various training and standards of GMP to ensure excellent quality standards for pharmaceutical products that will ensure the public gets more and regain confidence in the pharmaceutical industry.