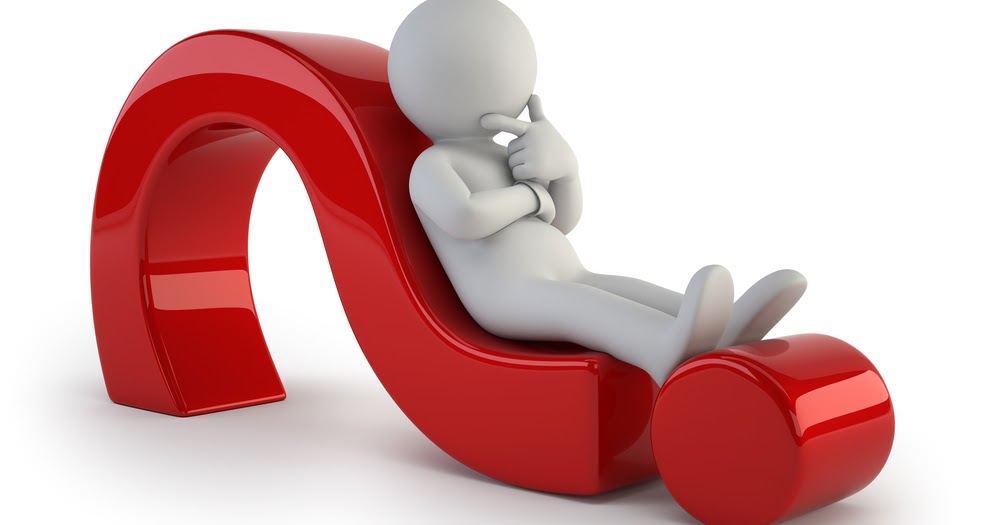
Out of specifications (OOS) in the Pharmaceutical Industry
In the pharmaceutical industry, Out of Specification (OOS) means a value that is either higher than or lower than a specified limit set under any regulatory documents, manufacturing procedure or quality control process. OOS results bring various consequences of poor product quality, imperiled patient safety, and noncompliance with regulatory requirements. For this reason, any form of OOS must be dealt with in a way that helps understand its underlying causes so as to give a proper foundation to manufacturing while at the same time maintaining the integrity of any product that may be affected. In this article, the author discusses the probable causes of OOS in the pharmaceutical firm under four heads: personnel-related factors, process-related factors, tool-related factors, and material-related factors.
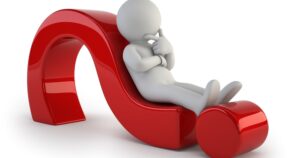
1. Human Errors
Out of specifications results in the context pharmaceutical industry are often due to human errors. These errors are materializable at any point of the manufacturing or quality check and control processes, including purchase and storage of raw materials.
a. Improper Training
Lack of competent staff training is in a position whereby personnel may be unwilling or incapable of executing required duties. This can be attributed to factors such as relative improper sample preparation, dozing off of equipment or even wrong interpretation of outcome results.
b. Documentation Errors
Document control is critically essential in the manufacture of pharmaceutical products especially in situations where strict compliance with standard procedures is required. Incorrect data entry mistakes, amiss records, or variations with batch production records lead to OOS results.
c. Violation of Standard Operating Procedures Thus
There is one major problem that results from noncompliance to those set standard operating procedures. Lack of adherence to validated procedures in the course of production is a common cause of OOS results, either through negligent act or otherwise.
d. Sampling Errors
Failure to select the right sample, contaminated sample or taking the wrong sample size or not covering the whole batch will lead to wrong test results.
2. Procedural Failures
Another type of requested documents is the procedural failure when the Process was incorrect not due to non-compliance with its provisions but because the provisions of the Process it self were incorrect. These can lead to variability in the manufacturing process which in turn results to obtainment of out of specifications results.
a. The major concern is that Process validation is documented and insufficiently executed.
What process validation does is to confirm whether manufactured products are meeting their required quality throughout the process. Inconclusive or substandard validation exercises can grossly affect a T&C process and outcome that these key signs such as process parameters such that means OOS results would be determined.
b. Ineffective Change Control
Any change in raw material, equipments or process needs to pass through a change control system which analyses the necessity and documents all changes. These changes include the failure to assess the impact of such changes can lead to a number of problems such as product inconsistencies.
c. Lack of Monitoring
For this purpose, regular surveillance of the vital process characteristics is required to identify potential variation. Sometimes, the absence of supervision can lead to quantitatively small deviations that reach critical values.
d. Poor Cleaning Procedures
Inadequate wash of equipment or facilities that are involved in any process can cause cross contamination which may affect the quality of products while analysis to may produce OOS results.
3. Equipment-Related Issues
The processing equipment in this sector is normally highly specialized. Problems with this type of equipment can be fatal to product quality given that they can cause OOS results.
a. Calibration Errors
Whenever there is production or testing equipment required then these must be calibrated frequently to achieve higher level of accuracy. If poorly calibrated, the instrument may produce inaccurate measurement and generate one out of specification.
b. Equipment Malfunction
Flaws in mechanical parts such as the wear and tear of the numerous parts in a manufacturing equipment, or peculiarities in the software controlling the manufacturing process, are examples of a source of variability.
c. Inadequate Maintenance
Implementing manufacturer standard operating procedures to maintain the equipment also becomes essential as failure to do so results to regular break down ages or simply poor performance.
d. The last factor
Environmental Control Failures, catches more complexities arising from the situation and is characterized by the following: A large number of pharmaceutical processes are either temperature or humidity or particulate sensitive operations. Mr. Carmack also noted that improper control of environment or HVAC systems can influence the quality of the products.
4. Material-Related Causes
The basic materials used in manufacturing pharmaceutical products have a major influence on the quality of the final products.
a. Raw Material Variability
This is because quality or composition of raw materials varies in different lots which in turn affect the quality of the final product. Such fluctuations may be caused by change in the supplier, test or in the raw material standards.
b. Contamination
Interferences in raw materials or intermediates with extraneous material like microorganisms, heavy metals or other chemicals are likely to cause OOS observations.
c. Degradation of Materials
Unfavorable storing conditions include exposure to high humidity or temperature, and can lead to impairment of content potency, chemical stability, or even decomposition in raw materials, intermediates or finished products.
5. Analytical Errors
Analytical testing as a form of quality control is unavoidable in the midst of enhancing the delivery of medications in the medicinal services business sector. This means OOS results can be occasioned by errors in testing methods or even the equipment used in arriving at them.
a. Method Validation Issues
As a primary rule, analytical methods must be shown to be appropriate for their intended purpose. It is a fact that any poorly validated method can so much generate wrong or uneven results.
b. Instrumentation Errors
If it is the case with analytical instruments then it can give wrong measurements and the same can be due to improper setting of instruments.
c. Operator Error
Sample preparation or analysis errors, pregnancy, stress, caffeine and alcohol intake, smoking, or a low calorie diet can affect a test’s outcome.
d. Reagent and Standard Issues
Sample contamination, use of expired reagents and standards or improper storage of these essential products causes testing inefficiency.
6. Stability-Related Factors
Stability testing therefore, determines the effects of environmental influences on a product. Consequently, failure in stability testing can lead to reporting of OOS results.
a. False Storage Information
When products or materials are not stored under certain conditions, the decomposition of such products hastens and this often leads to out of specifications results.
b. Inadequate stability.
Over the years, a number of Stability Studies have been conducted but large number of them fails to show adequate stability. Lack of conductance or inadequate stability studies might not even predict the stability profile of the product or the shelf life of the product.
c. Packaging Failures
Materials or packaging designs that do not shield the product from influence can impinge on stability or alter it in some way.
7. External Factors
There are also factors outside the management’s control in the manufacture of pharmaceuticals where OOS results may be realized.
a. Supply Chain Issues
Delays, unverified suppliers, insufficiency of conditions of transport, it is all can influence material quality in supply chain disruptions.
b. Regulatory compliance change.
Sometimes, changes in rules or regulations may make earlier given specifications or methods to be no longer compliant with the current requirements hence resulting in out of specifications results.
c. Natural calamities or emergencies
Situations like power blackouts, floods, or even an earthquake will completely mess up the manufacturing chain and there is a high likelihood that this will disrupt quality standards.
Dealing with out of specification results: your go to guide
According to requirements, when an OOS result is obtained, one should proceed through a step by step approach to investigate the occurrence and find out the necessary corrective and preventive actions (CAPA).
1. That is why the recommendation for the committee is a thorough investigation.
Analysis of the records of batches and testing results.
Revise retained samples, so that the results are corroborated.
Differentiate the possibility of contributing factor which may include equipment, people and processes.
2. Again we find that all the corrective actions had been rightly implemented by the management.
Remedial actions refer to bringing an end to the problem; the actions taken may include personnel retraining, equipment recalibration, or procedure modification.
3. Setting Up of Preventive Measures
Preventive actions are directed at non-recurrence, for example, in training, in validation of processes, or in monitoring tools.
4. Documenting Findings
That is why sometimes the necessity of maintaining detailed records of investigation, results, and taken measures becomes obvious in terms of compliance and subsequent improvement.
Conclusion:
It would be helpful to explain possible origins of OOS in relation to the pharmaceutical sector, to improve product quality and security for consumers, and to satisfy legal requirements. Through cause analyses, strong formal corrective/preventive actions, pharmaceutical OOSs can be reduced and a viable improvement cultural set can be developed. Some of the strategies that would be employed in order to achieve this goal include training of employees, enhancement of the organization’s technological capacity, high standards in quality assurance mechanisms.