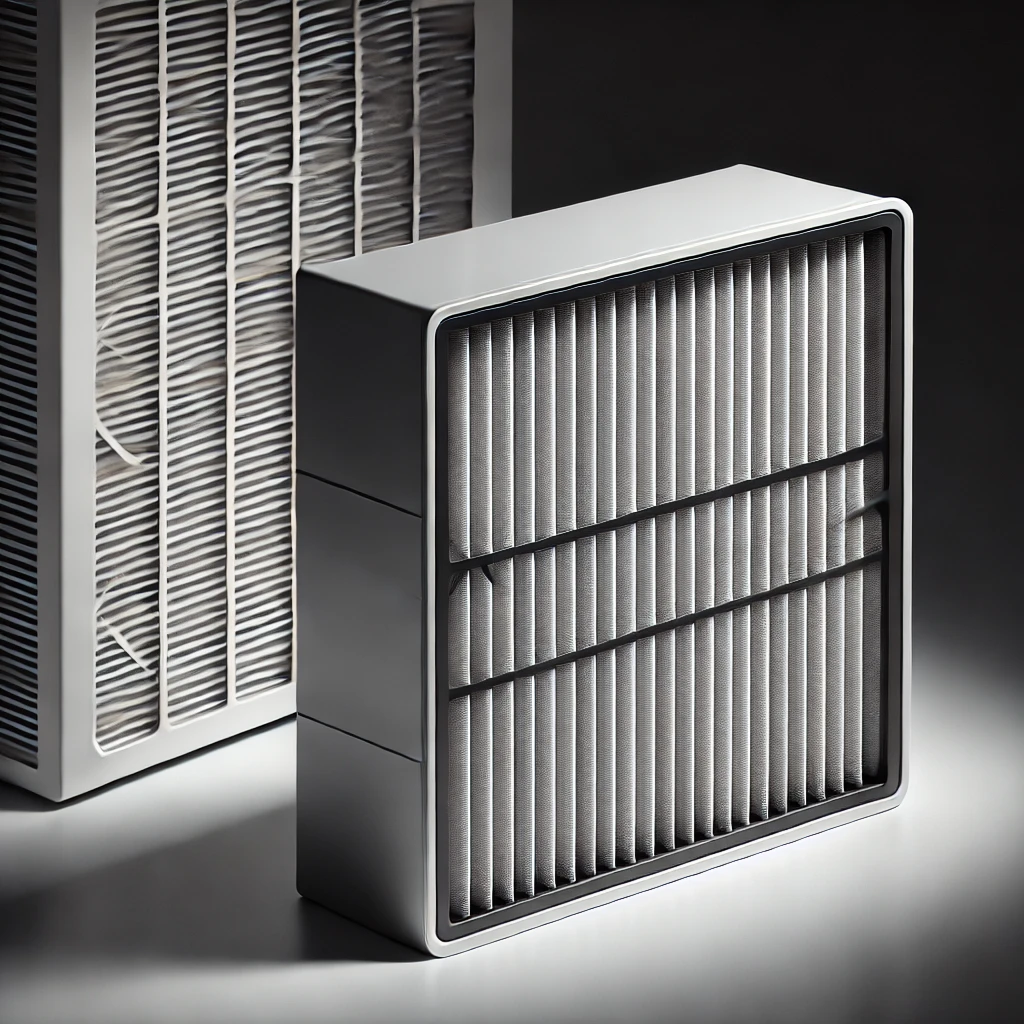
HEPA Filters a detailed Introduction, and Use in Pharmaceutical Industries
Introduction
High-Efficiency Particulate Air (HEPA) filters have become a cornerstone of air purification technology in various industries, particularly pharmaceuticals, where maintaining a contaminant-free environment is critical. HEPA channels are more often than not glass fiber or cellulose and glass fiber materials.
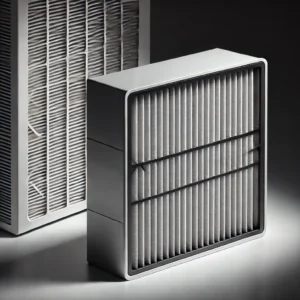
For tall temperature utilization reason made channels steady at temperatures up to 350ºC, are accessible in spite of the fact that it ought to be famous that these channels, utilized in sanitizing burrows, are known to shed particles amid the warming and cooling stages and as it were meet HEPA channel criteria beneath steady temperature conditions.
A High-Efficiency Particulate Air (HEPA) filter is an advanced filtration system that provides enhanced Micro-particles filtration and enhanced air quality through the employment of a tightly packed mass of randomly arranged fibers mostly made from fiberglass or synthetic fibers to trap all particles as small as 0.3 microns with 99.97% efficiency. HEPA filters for use in Pharmaceutical manufacturing or sterile manufacture should be specified to the suppliers with respect to the efficiency of the media for retention of particles of 0.3 µm median diameter. Specifications of less than 99.97% efficiency must not be used.
Mechanism of HEPA Filter Working
HEPA filters work through three primary mechanisms, number one, Interception is whereby particles moving in the airstream get to a close range with a fiber then they stick to the fiber due to flight paths. Then Impaction captures larger particles which cannot change directions with fibers due to their mass, which ultimately results in impact with filter material most especially in instances where there is high air flow rate. While, diffusion is useful for particles of size less than 0.1 microns, this move randomly due to Brownian motion and get even closer to the filter fibers therefore improving chances of being trapped. Both modes function in concert to effectively trap particles of differing sizes such as dust, pollen, molds, pet fur, some bacteria and viruses etc. Some higher efficiency with particles even to the size of 0.3 microns known as ‘most penetrating particle size’ in which all the three mechanisms combined will likely provide a very high efficiency. Common in the medical field, aviation, manufacturing, and homes where cleanliness is of high importance, and in hospitals for instance operating theaters, clean-shops, and air purging of residential and business spaces. Although widely effective, HEPA filters are not without their drawbacks; they cannot eliminate gases, smells or volatile organic compounds (VOCs) which are best handled by other filters such as activated carbon filters. Any filters which can be used several times have to be changed or thoroughly washed, because their clogging functionality, lower air filtering and airflow. However, HEPA filters are one of the basic technologies used today in air purification and the results prove to highly alleviate the problems of airborne contaminants and bring greater benefits to the health of individuals.
Design and Structure of HEPA Filters
The designing part of a HEPA filter is quite complex and very effective in achieving the kind of efficiency that this filter is capable of. The filter itself can be a mat with a huge number of spiral, often glass or polymer structure randomly directed microfiber, or a combination of both. The fibers themselves are very thin: in most cases, their diameter is less than one micron, although the fiber length can reach up to fifty micrometers. Accordingly, the fiber material for the composite particle is selected according to chemical resistance, mechanical properties, and particle retention. To ensure that the fibers do not break off when exposed to the airflow and to provide enough stiffness, they are bonded in a lattice like structure. It also creates a favorable manner in which filtration is enhanced because it increases in the area through which air flows. Thus, the probability for the particles to pass into contact with the fibers, and be retained, is increased. Another factor is that the more fibers a HEPA filter has, the denser they are – the greater its efficiency is. The thicker the thickness of the filters, the more layers they have of the fiber, and the more chances for trapping the particles.
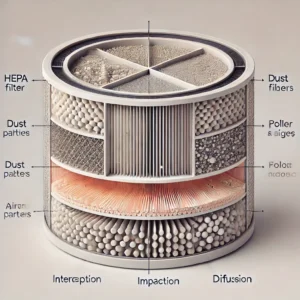
These fibers are many-layered and have different patterns for increasing the filter’s efficiency of the removal of a range of small particles. Around the microfiber mat there is a sequence of restraining layers. The outermost layer is commonly include synthetic polymer or other material which is suitable for shielding from moisture or other components. This layer serves to avoid the microfiber made cloth from being blocked or from being overloaded with moisture that may affect its trapping of particles. However, some HEPA filters have an additional layer that is responsible for filtration of hair, dust, pet dander: this layer serves as a pre-filter and increases the durability of the microfiber mat. The efficiency of the filtration means that to facilitate the free flow of air through the filter; HEPA filters should possess low resistance to air flow. Obviously, the engineers who are working on designing HEPA filters do a very good job at counting the number of fibers that must be present and the actual spaces between them where bacteria can perfectly find a place to develop. This serves to allow the filter perform its work in trapping dirt and particulate matter associated to it, but yet not interfere with the air quality in that room in which the filter is used. In total, the construction of a HEPA filter is exceedingly complex with the objective of the filter to clean the air through the expulsion of unwanted small particles. Different material, pattern and layers’ combination make HEPA filters very useful in as many application areas as possible, enhancing the quality of air we live in.
Types of HEPA Filters
HEPA filters are of several types depending on efficiency and construction of the filter, detail of which are as follows. The normally used HEPA filters are pleated HEPA, rigid panel HEPA and cylindrical HEPA. The filtered are built from pleated fiberglass and/or polypropylene that are folded reducing the thickness to create more surface area and therefore more filtration. This design enables them to capture the particles based on a force that brings the particles to settle at the base of fibers.
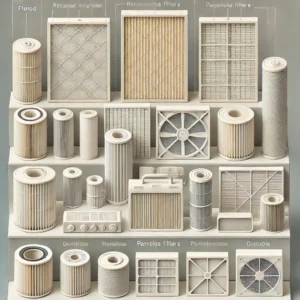
HEPA filter is a rigid panel of fiberglass, polyester, aramid fiber or metal that forms a net like pattern. HEPA filters that are cylindrical have many layers of thin pleated metal covers contained in a cylindrical metal casing with a large surface area that provides the depth of several shallow pleated units in a compact container. According to the efficiency index (MERV (Minimum Efficiency Reporting Value)), HEPA filter can be grouped into different classifications. MERV ratings are between 1 and 20, the higher – the better, means this air filtration is more effective. HEPA stands for High-Efficiency Particulate Air filters which generally come with a MERV rating of 17 to 20, which allows the greatest extent of particle filtration. There may also be added elements such as activated carbon or ultraviolet lighting incorporated into some of the latest HEPA filter.
Use of HEPA Filters In Pharmaceutical Industries
The pharmaceutical industry is quite helpful in using HEPA filters as they can remove the particles as small as 0.3 microns with standard efficiency of 99.97%. This feature is aimed at maximizing the quality of air circulation in the manufacturing, processing and packaging sections of the pharmaceutical industry and eliminating lint, dust, bacteria and viruses. The following are some applications of HEPA filters in the pharmaceutical industry:
1. Sterility in manufacturing: HEPA filters ensure that there is minimal contamination during production of drugs, vaccines and other medication, in clean producing areas for instance clean rooms and manufacturing facilities. These filters are crucial in protecting products made a concentration of any type from happening.
2. Aseptic processing: I used for products that were aseptically sterilized, and then aseptically filled. This process is useful because it prevents the bunch of medications from contaminations and keeps the actual effectiveness of the medications.
3. Air purification: HEPA filters are used for cleaning the air in pharmacies, laboratories and other premises of the pharmaceutical sector. Besides shielding the products from contamination by airborne pathogens, it would promote a cleaner environment for the workforce.
4. Filtration in respirators and protective equipment: Respirators and protective gears like face masks and air purifying helmets and head gears are created with the use of HEPA filters. This assists in shielding the workers from an unexpected intake of particles that include pharmaceutical dust, viruses, and bacteria.
5. Filtration of process gases: At other times, HEPA filters are used to filter gases which are used in manufacture of products like nitrogen or carbon dioxide. This assists in checking on the purity of the gases which are used in product manufacturing process hence a quality output.
6. Microbiological control: The efficiency of removing micro-organisms in the pharma industries highly relies on HEPA filters. They are installed in HEPA filtered cabinets for microbiological applications, in air showers and clean air transfer zones for controlling carryover of contamination between clean and dirty zones.
So many areas in the pharma industry uses HEPA filters from the cleanliness of manufacturing, all the way to air filtration to product quality. Their high efficiency and capability to capture small particles make them an important part in safety and effectiveness of medication products.