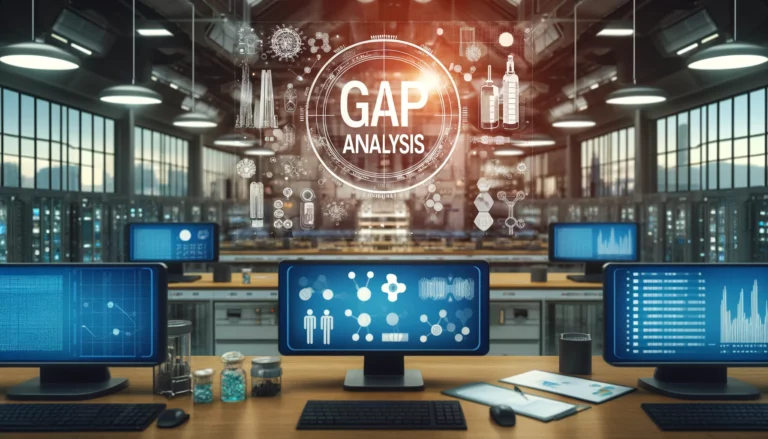
Gap Analysis for Regulatory Compliance in Pharmaceutical Industry
For pharmaceutical corporations in the field, compliance is more than just a legal responsibility because it is essential to product safety and patients’ well-being as well as customers’ confidence in the products they buy. Various bodies like the FDA in the United States, EMA in Europe, and WHO at worldwide level outline various policies and standard that firms in the production of drugs must adhere to. Consequences for noncompliance may include legal action, recalling the product and loss of the company’s reputation.
A regulatory compliance gap analysis is an essential method that serves to determine the conformity of activities and actions of a pharmaceutical company with the standards required and existing regulations. It helps in identifying some of the non-conformities which if not corrected are likely to lead to disaster for an organization. In this article we are going to learn more about the concept of gap analysis pertaining to the pharmaceutical industry, its significance and how to accomplish it.
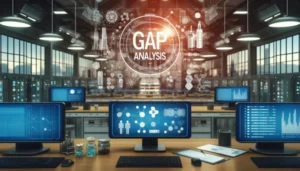
What is Gap Analysis?
A gap analysis is a business modelling technique which is commonly used to identify the difference or gap which exists between a firm’s existing practices and the best practices or standard practices that can be implemented within an organization. The analysis of gaps in the regulation mean that in the context of regulatory compliance in the pharmaceutical sector this involves the processes of matching the organization’s current practice in relation to the code of practice provided resulting in non-compliant areas and a work plan to cover those.
It is recommended to conduct a gap analysis because it remains the best way for pharmaceutical companies to continuously update themselves on those regulations and standards in order to reduce the risks of getting it wrong and ensuring that its products achieve the right quality.
When it Comes to Regulatory Compliance, How does Gap Analysis Matter?
More so, in the pharmaceutical industry regulatory compliance is a non-negotiable thing and should be strictly adhered to. Before a company can sell its products, several procedures must be followed and maintains a certain standard. Gap analysis is essential for the following reasons:
Mitigating Risks: Negative consequences resulting from failure to meet the requirements include product recall, legal litigation and harm to the company’s image. A gap analysis assists in making sure that the company has not been deviating from various requirements which should be taken care of immediately.
Ensuring Safety and Quality: Bodies like the Food and Drug Administration (FDA) and the Europe Medicine Agency (EMA) set down measures to ensure that drugs and other pharmaceutical products bear very high safety and quality standards of health. This is important for the pharmaceutical organizations in order to make sure that they develop suitable products free of defects or those that do not pose a harm to society in accordance to the following standards which gap analysis assists the organizations to remain in harmony with.
Preventing Costly Consequences: Punishments include fines legal fees, and losses that may come from noncompliance among employees. An effective Compliance risk gap analysis enables organizations to assess for compliance prospects before they transform into problems that are expensive to address.
Improving Operational Efficiency: Consequently, having an understanding of the compliance risks and rectifying them provides to companies increased efficiency of functioning, better regulation of performance, and enhanced effectiveness in different procedures employed.
Keeping Up with Regulatory Changes: There is always improvement on the regulations governing the operation in the pharmaceutical industries. Externally, the gap analysis enables organizational management to discover various regulatory changes within the business environment and make sure that their practices reflect the changes.
An Applied Guide for Conducting Gap Analysis for Analysis for Regulatory Compliance.
To perform the gap analysis, the following structured processes are followed; Below is a detailed guide on how to perform a gap analysis:
1. What is meant by Regulatory Requirements and Standards?
The first approach when conducting a gap analysis is to determine the standards that must be met by the pharmaceutical organization. This includes familiarizing yourself with local, national, and international regulations, which may include:
Good Manufacturing Practices (GMP): Trade practices that concern the production standards and quality assurance of manufactured drugs.
Good Distribution Practices (GDP): Policies and procedures providing a standard and quality product in term of purity and safe during the distribution of drugs.
Good Clinical Practices (GCP): A guide to the design, conduct, and reporting of clinical trials.
FDA and EMA Regulations: Exactly formulated policies formulated by the FDA and EMA encompassing rules that the pharmaceutical firm has to follow with regard to drug approval, labeling and post-market monitoring.
International Council for Harmonization (ICH) Guidelines: General provisions for experimentation: guidelines for toxicity testing of pharmaceuticals, stability studies and related concerns in Regulatory submissions.
Every regulatory body or guideline describes the qualification requirements necessary for compliance clearly. Understanding these requirements to their depth is essential in establishing anomalies in the existing processes.
2. Assess Current Practices and Processes
Based on the regulatory requirements, the next step is to evaluate the existing state within the company. This includes:
Internal Audits: Internal audits or assessments of the firm’s production, quality assurance/clinical research, shipping, and labeling processes.
Reviewing Standard Operating Procedures (SOPs): Reviewing the current standard operating procedures of the company, to determine conformity to the current regulation. Fre’s perspective of the necessity of having the sop’s is a detailed process in production, testing, packaging, and distribution.
Evaluating Training Programs: Auditing training to confirm that the requirements of all regulations and standards have been conveyed to all people.
Examining Records and Documentation: That records relevant to production, quality assurance, supply chain and that of clinical trials are kept well, comprehensive and accurate. Documentation must be well-documented for the regulatory audits to be done properly.
3. Identify Gaps in Compliance
The next step after that is to assess the regulator, that is what gaps may exist between the current business practices and the regulation. This can be done by comparing internal processes against the following:
Regulatory Guidelines: Are all the practices of the company good in terms of the regulatory provisions of the bodies of the country and standards?
Industry Best Practices: How well does the company follow best practices applicable in pharmaceutical manufacturing, testing or distribution?
Quality Standards: To what extent does the company conform with the quality control systems set up by the regulating bodies as well as other organizations?
Common gaps in compliance may include:
- Lack of compliance with GMP or GDP regulation
- Omission and distortions
- Lack of, or out-dated training programmes
- Inaccuracy in labeling The labeling practices of many organizations do not conform to this guideline.
- Consequently, risk management strategies are not undertaken.
- This lies in the roulette-like variations in the values that portrayed results clinical trials data.
- The next process is to determine these gaps as a from which an action plan to address the gaps can be developed.
4. Develop an Action Plan
Subsequent to assessment of compliance deficiencies, further action consists of creating a strategic action plan. This plan should show the action plan required to address the above mentioned gaps with a goal of placing this company into full compliance with the law. The action plan should include:
Specific Actions: Describe precisely what operational steps have to be implemented in order to reduce or close each gap. For example, there may be a gap in GMP compliance in cases where the company must update the manufacturing process.
Timeline: Ensure that implementation of the corrective actions is put in a proper timeframe. There are those that call for urgent implementation and there are those that may mean operational for sometime.
Responsible Parties: Responsible persons or departments for each corrective action should be determined. This makes the parties answerable and makes certain that all activities are done a venture’s stated timeline.
Resources Required: Determine the factors (such as manpower, funding, tools)” required to carry out the corrective actions.
Monitoring and Evaluation: Approach on how the corrective actions would be monitored and Major compliance gaps evaluated to determine that corrective actions would have effectively closed the compliance gaps.
5. Implement Corrective Actions
After establishment of the action plan, it becomes possible for the company to implement the corrective actions. This may involve:
Process Improvements: Bringing manufacturing, testing and distribution in conformity with the latest regulatory control.
Revising SOPs: This involves reviewing and changing the current standard operating procedures to address the frequent emerging changes in regulatory environment and encourage implementation of new trends on the market.
Training and Education: For dealing with the new procedures and regulation, the final strategy that can be adopted is educating the employees who needs to implement the changes through training activities.
Documentation and Record-Keeping: That all records necessary are kept, accurate, up-to-date and easily retrievable in case of a future audit.
6. Measure Performance Changes and Make Reassessment Audits
After a company has put into place corrective measures then it is required to assess the viability of the interventions. Such works include post-audit exercises primarily to ensure that the gaps have been closed and that the company is in absolute compliance with all the regulations. Another requirement is that such reviews should be conducted periodically to check compliance afresh.
7. Continuous Improvement
The legal and professional standards are not set in stone and are often upgraded so, pharmaceutical organizations are required to balance improvement. Conducting of the gap analysis should not be done occasionally but rather should be a routine in the organization to confirm that the firm operates within the legal requirements and best practices concerning any changes in laws.
Conclusion
Pharmaceutical regulatory compliance assessment is highly dependent on the gap analysis process. By pointing out the existing differences between the regular business practices and the laws the pharmaceutical companies can start making efforts to reduce the distance between them. The process of gap analysis involves outlining of regulatory demands, survey of existing practices, identification of deficiencies, leading to an outline of an action plan, putting into practice the required changes, and ongoing assessment of the results.
Regular gap analyses make it easier for the pharmaceutical firms to be in compliance with the changing regulations, have quality products, and keep their reputation with the regulatory bodies and the customer. Followed correctly, this approach will serve as a chemical map directing the pharmaceutical companies in following Research compliance requirements and offer trustworthy and useful products.