Pharma
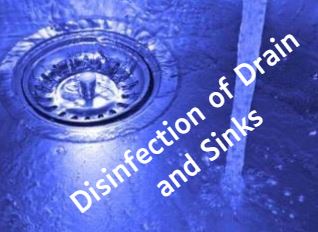
Disinfection of Drains and Sinks in Secondary Pharmaceutical Facilities
The major source or contamination in non sterile products, particularly aqueous products such as creams, oral liquids, arises from water borne organisms (e.g. Pseudomonas aeruginosa and other potentially objectionable organisms). These organisms are found commonly in drains, wash bays and sinks and their control is of critical importance. Although the regime of cleaning and disinfection is of great importance, the good design of drains, sinks and facilities to reduce contamination and its spread is of even greater importance.
- There should be an air break between floor drains and machine drains. Floor drains should be adequately trapped.
- Pipes entering drains, tun dishes and sinks should be designed to avoid excessive splashing and creation of aerosols of liquid since these are a major source of spread of contamination. Similarly taps to sinks should be
controlled to avoid excessive splashing. - Drain surrounds should be designed for easy cleaning and to avoid trapping debris. Sloped surrounds, well fitted stainless liners or collars (removable) and in some cases caps may be useful. Tiled and grouted surrounds are not ideal.
- Air flows within the facility should be designed to take any aerosols or droplets created around drains or sinks away from critical process operations and towards extract. It is frequently found advantageous to design higher air flows or negative extraction within wash bays to remove the potential aerosols of contamination.
- Where horizontal laminar flow units are used to protect washed items prior to wrapping, it is important that the sink area itself does not have laminar flow across it. The reason again is the potential spread of aerosols of contaminated liquid from the washing process.
- Heated traps may be used, where appropriate, and can be effective in controlling contamination in sink drains. However the control of such heated traps is extremely important and if not performed correctly may be counter productive in control of the drain trap. It is important that all the water in the trap is raised to 70°C or above, the process is sufficiently long to ensure effectiveness, the liquid is not boiled (even more importantly is not evaporated completely as this will produce a direct air route from the main drains) and the heating process is regularly carried out.
- Problems with operational failures (burnt out elements, non reliable control systems) has seen a reduction in the use of heated traps.
- The movement of water in drains can significantly change the level of contamination, infrequently used drains with stagnant water representing a greater risk than drains with regular use and large volumes of effluent passing through it.
- The use of disinfectants within drains may be required from time to time but has limited value due to the contact with large amounts of organic matter and dilution leading to rapid inactivation. As such their effectiveness is often relatively short and the design and management of facilities to reduce risks from drains/sinks is therefore very important.
- When disinfectants are used, measures can be taken to improve their effectiveness by means such as: Pre-cleaning with a suitable detergent solution. This must be compatible with the disinfectant which is going to be used. Flushing the drains with copious quantities of water, hot if possible, before addition (steam lances are sometimes used). Some caution is needed if using chlorine based disinfectants which are not suitable for hot situations. Leaving disinfectant solution in place when the drain is not in use (e.g. overnight) to reduce dilution and prolong activity. It may be necessary to use a specific agent for a specific contamination problem.
Zulkifal
0
Tags :