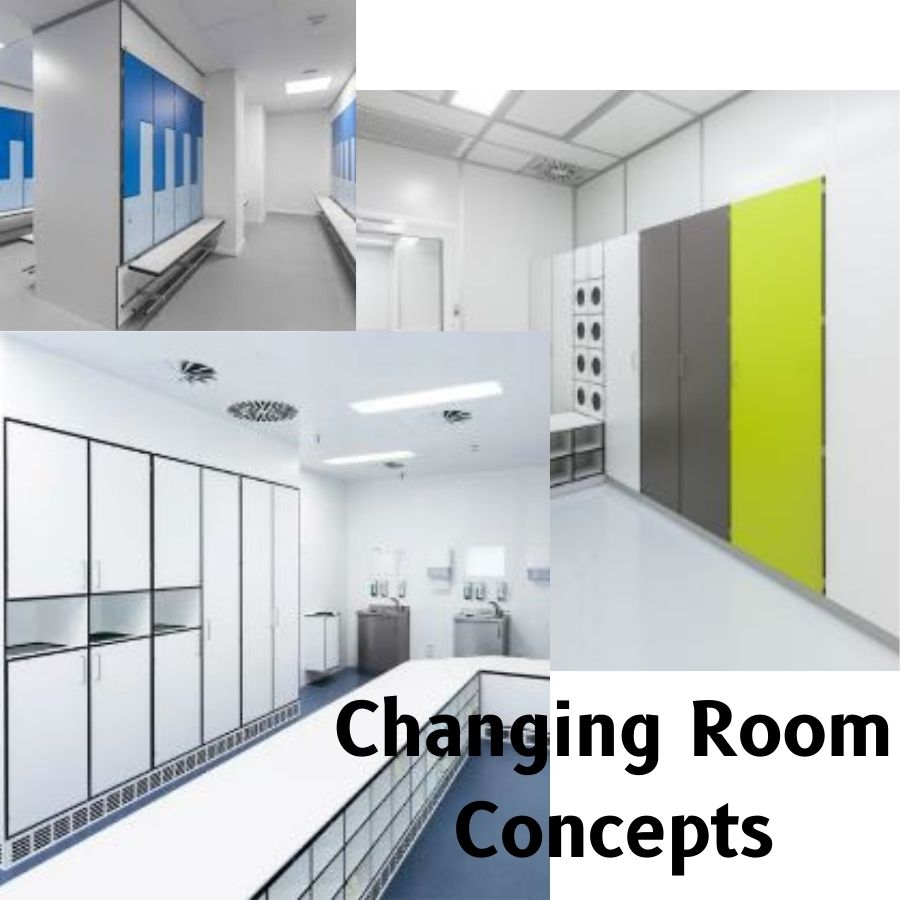
CONCEPT FOR CHANGING ROOM IN PHARMACEUTICAL FACILITIES
Introduction
The optimal design of a changing facility is dependent on
- the number of people required to change at the same
- the clothing regimes both inside and outside the designated production
Changing Rooms
Changing rooms are provided so that personnel can remove their outer garments before entering the designated production area, thereby preventing outside contamination being carried into the department and creating a risk to production quality. In the same way, production uniforms are retained inside these changing areas to ensure that production materials are not transmitted outside the production area itself. Changing rooms should not be used for the transport between zones of production materials or equipment. Changing Rooms are normally divided into outside (Dirty) and inside (Clean) sections. Each section must allow sufficient space for personnel to remove and store the necessary garments required beyond the changing room. Arrangements must be made for storage, laundering and disposal of new and used clothing components – Coats, Shoes, Overshoes, Gloves, Caps etc.- as required by the production department and for mirrors, signs and displays to ensure that personnel are appropriately dressed before they leave the room.
Where the contamination risk across a changing room is found to be severe, electrical interlocks may be used to prevent the opening of one door while the other door is not fully closed. Such interlocks must be automatically disabled if a fire alarm condition is detected. In less severe situations an audible alarm may be found to be sufficient. Other measures, such the complete physical separation of clean and dirty sections may be introduced if the contamination risk to production or to personnel is particularly great. The Changing rooms are to be conditioned to the higher standard of the areas separated by the change. The environmental air system supply to changing rooms should be designed to provide an airflow from the ‘Clean’ side to the ‘Dirty’ side. Experience shows that changing facilities for groups of 30 people or less are easier to supervise than larger ones.
Changing Barriers
Changing barriers can be created by fixtures (benches) or by static indications (lines) and must be positioned so as to separate the ‘Clean’ and ‘Dirty’ sections. Personnel must be trained in the correct method of dress and passing the barrier in accordance with an SOP which should make extensive use of photographs to illustrate the procedure.
Lockers
Individual lockers should be provided for each person in which they can retain the street clothes or uniforms worn prior to the change. It is recommended that storage is provided on each side of the barrier so that contamination is not passed between different garments. Lockers can be purchased in continuous rows of several units, with benches and shoe lockers if needed. They should be installed at a level above the floor to enable cleaning to be carried out beneath them. To prevent the accumulation of dust above the lockers, they should have sloping tops or be enclosed to the ceiling. This common space can be used as an exhaust plenum to collect air drawn through the lockers from the changing room so keeping clothes in a comfortable condition for use. In severe or very wet climatic conditions, heating elements below the lockers can be added to warm and dry the contents.
Location of Toilets, Showers & Hand Basins
Where it is required to include these facilities in the changing module, they should be positioned on the outside (dirty side) of the changing barrier – whether physical or indicative. Air extracted from these cubicles should be discharged to the outside environment and not re-circulated to the production areas.
Laundering of Garments.
In house laundering of garments used in Grey Zones is advisable. Contract laundering facilities may be used
- if there is sufficient assurance that garments have been cleaned
- provided that product risks are not ‘exported’ to the contract laundry, exposing personnel there to highly active materials.
- provided there is no risk of cross contamination from other companies’ laundry in the same contract facility.
In house laundering of garments used during the manufacture of B -lactam and highly toxic materials must be undertaken in their own segregated facilities. General factory clothing worn by operators in Factory Black Zones may be contracted out to a general laundry. If significant spillage or exposure to product or active material occurs, the garments should be laundered following procedures for garments used in Grey Zones.
SOP’s /Contracts for all Laundering Activities
An external laundry should be audited and approved by QA as a supplier. There should be an SOP, or in the case of external laundries, a written contractual agreement which covers
- Safety of laundry personnel in terms of types of contaminants to be found on
- Avoidance of mixing of GlaxoSmithKline and garments of other companies at any stage of laundering.
- Segregation of clean and dirty.
- Segregation of dedicated
- A requirement for written approval for changes of water quality, air quality, wash cycles, or detergents. Routine visual checks of the garments.