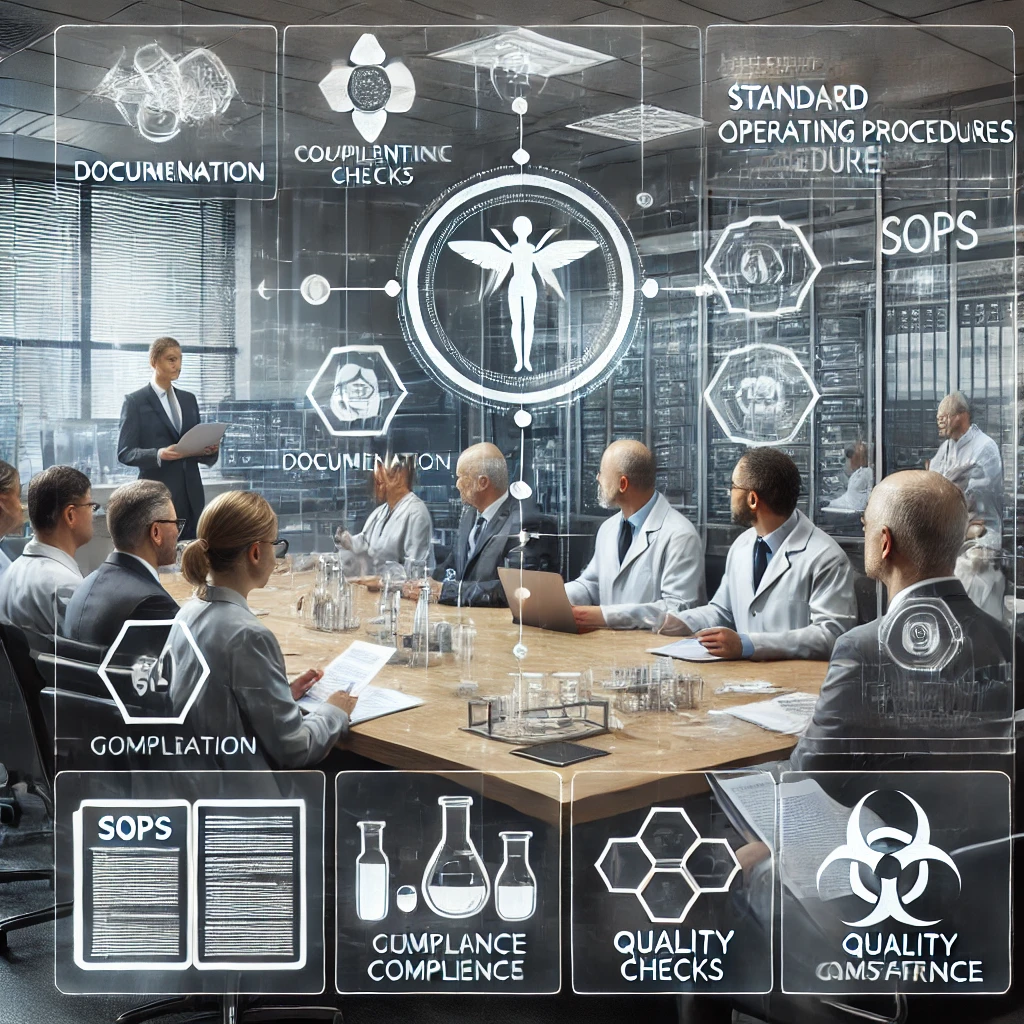
Writing Effective SOPs in Pharmaceuticals
1. Introduction
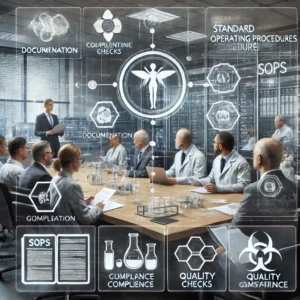
Standard Operating Procedure (SOP) as used in the pharmaceutical industry is an important document that is designed to provide details of a specific process or operation and dictates proper means to perform that operation. Lastly, SOPs are very useful and also when it comes to compliance with set regulations, but SOPs give directives to employees to adhere to and have lastly. It’s very crucial for any pharmaceutical company to write good SOPs. This document will provide a guide to writing good sop especially in the pharmaceutical industry.
2. Scope
This SOPs apply on all the employees who work with the writing, reviewing, and implementation of the SOPs in the pharmaceutical industry. This is not intended for the use of a particular department, but for employees from the lowest rank within the organization up to the executives.
3. Responsibilities
Non-compliance and reporting of issues must be done by the employees while improvement of the SOPs is expected from every employee. The QA department oversees SOPs to make sure that the SOPs are good and complete enough, and most importantly that they are up to date for the organization.
4. Documentation
4.1. Numbering and Title
All SOPs should be numbered and named for easy identification and tracking since there will be many of the documents. The number should be linked with the particular process, the title – with the material to be published.
Example: SOP-001, Active Pharmaceutical Ingredients Preparation
4.2. Format
SOPs should be written in clear, concise language, with a standard format that includes the following sections:
a. Purpose: This statement should give a clear idea in a couple of word about the purpose of the SOP.
b. Scope: A description of the tasks in the process, the systems or piece of equipment in which the SOP is expected to cover.
c. References: All materials that are connected with the developed procedure, such as documents, regulatory acts and guidelines that should be followed.
d. Roles and Responsibilities: A listing of companies or individuals who will be in any way involved in the process and their functions.
e. Procedure: A narrative description of the process written in bulleted points and in clear numbered instructions.
f. Equipment and Materials: It means the list of all equipment, tools, and other necessary materials that would be used in order to implement the process.
g. Quality Assurance: A part with information on the types of quality controlling measures that can be taken additional to the acceptance criteria of the process.
h. Revision History: A record book in which the changes made to the SOP have been recorded along with the date when the change was done or who changed it.
5. Review and Approval
Any SOP developed prior to being finalized must be sensitive to senior staff in the organization for examination and endorsement. This commonly involves the QA manager, department manager of the process under concern as well as any other body that may need to approve the document.
6. Training and Implementation
Once an SOP has been drafted and approved all employees exposed to its content and the requirements within must go through it. It may be training by face to face teaching, individual coaching or through training materials that a person trains through the internet.
After learning should follow an assessment to determine the level of understanding of the SOP and the ability of employees to perform the process. Equally performing well on the SOPs and being supervised and monitored that ensure employees are following the SOPs.
7. Monitoring and Maintenance
Frequently the SOPs have to be updated and reviewed periodically to be effectively carried out and to incorporate the most recent information. This should be done at least once a year, or when the company experiences any changes to the process or conditions under which the process is exercised.
The following guidelines have to be followed with reference to any changes which are made to an SOP: The change must be assessed and authorized by the correct person/s, and the change must be recorded in the revision history section of the SOP. This implies that employees should undergo through training basically on the new developments of the SOP in their organization.
8. Conclusion
Development of proper SOPs is essential because it will facilitate proper implementation of process in the industry. This document will demonstrate organizations that, through careful adherence to the steps outlined above, their SOPs are easier to understand for the employees and provide them with excellent guidance through the processes. It will also enhance product quality, compliance to the law, and organizational success in the end.